Hi all!
I'm not sure that's the right sub forum for this object
I'm building some extreme binding post for speaker, usable even as replace for welding machines or Others high current applications.
I used 1" - 25mm brass rod, m10 threaded cap, 10mm hole for a 3\0 avg cable, overrated for an home speaker.
I used my last experience with binding post, then:
- decided to knurl the knob, m10 thread can be hard when cable inserted, now it's nice to use fingers instead of a tool.
-large insert hole, 10mm instead of 6mm, useful with particular high end cables
-teflon thick insulators, on 15mm aluminum frame, maybe the best insulator, with a sturdy frame.
I'm building them as a gift for a friend that is building some very good speakers, I think I will make some couples more for me, I need to rebuild 2 amp frame and question is : why use commercial poor type binding post when I can use some huge custom made one?
I will not tell you that they sound better than other (high priced) binding post, they're just connectors made of good material, contrarily to many magnetic copper and brass found!
It's my taste that a great detail like this can give the right accent
Ps: next thing to do is the body of connector
Saluti
Stefano
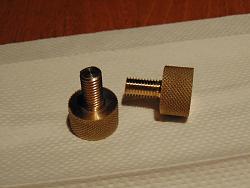
Bookmarks