I have a small MEAD H/V 6" Rotary Table and I needed to adapt a small 3" Sherline chuck to it. The chuck has 3/4-16 threaded back and the rotary table is an MT2 Taper.
I used a piece of 11/16th diameter aluminum to make the spindle adapter, you 'll see why so small shortly. Chucked up in the lathe I set the angle tool post at about 1.5 degrees and started cutting.
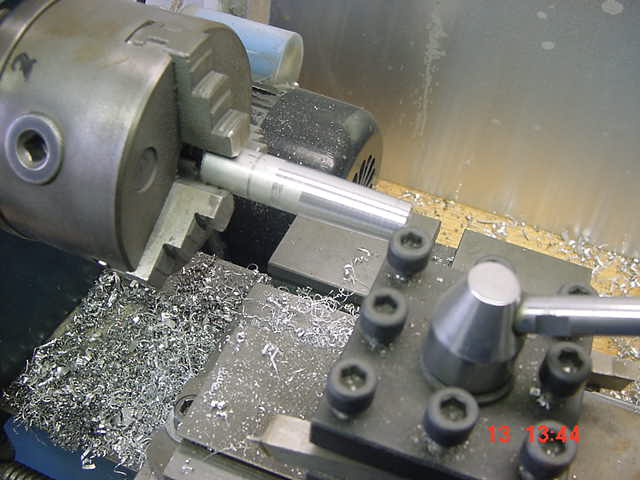
Once I had it close I started checking the fit and adjusting the angle until it fit in nice and tight with no slop. I don't really know what the angle is but it is a little under 1.5 degrees on my tool post.

I drilled and tapped the back side for a 1/4-20 "draw bolt" to pull it tight into the table.
I had a few miss-steps getting this project off the ground. Trying to thread the end, with that 3/4-16 die was not working. I couldn't get the thread to be parallel to the body of the rod. The only solution was to put on the taper THEN thread it in the lathe with the adapter slipped into the MT2 tailstock.
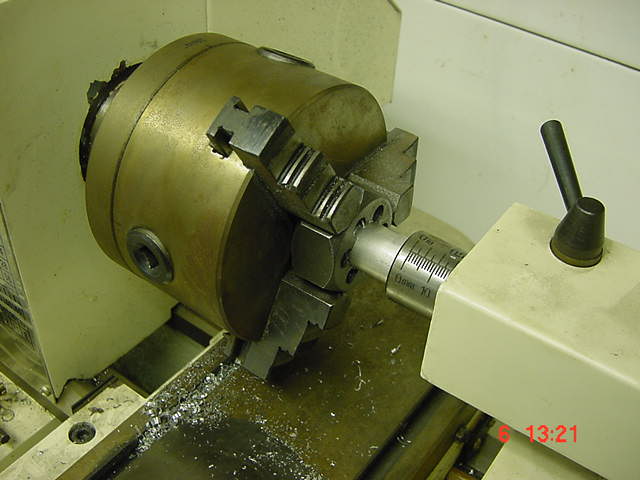
This worked well and got me a concentric thread. I left the threading die "loose" in the lathe chuck so it could follow the thread out of the chuck. With the tailstock locked down I rotated the lathe chuck by hand and got the die threaded on about the length of the die.

Next post
Bookmarks